Liquid Waste Disposal Perth is a crucial aspect of industrial and commercial production. Understanding the processes and regulations involved is important, as improper waste disposal can cause serious environmental harm.
The first step in liquid waste disposal is treatment. This process removes pathogens from the waste and makes it safe for disposal. It can be done using physical methods like filtration and sedimentation or biological methods.
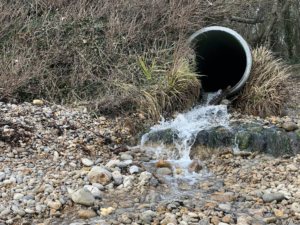
Depending on the type of liquid waste, the first step may be screening or separation to remove large particles and non-organic contaminants. The waste can also undergo biological or aerobic treatment to break down organic pollutants and nutrient compounds. This is usually done with the help of microorganisms like bacteria and fungus. In more advanced treatment facilities, tertiary treatments are used to further break down the waste and create useful byproducts. The process often involves oxidation, chemical oxidation or thermal desorption to reduce the concentration of harmful substances in the wastewater.
Another important step in liquid waste disposal is characterization, which involves testing the waste to determine its characteristics and identify any contaminants. This information will be used to select the appropriate waste disposal methods. It’s also important to keep records of this process for compliance purposes.
Safe transport of the liquid waste to its treatment or disposal facility is crucial. Specialized containers and vehicles are used to prevent spills and leaks that could contaminate the environment or harm workers. These containers are also marked with warnings and handling instructions to minimize the risk of accidents.
Hazardous liquid waste is typically transported to a processing facility in sealed tanks or other large vats. The tanks are monitored to ensure that the liquid doesn’t reach other areas or cause any environmental hazards. The tanks are also used to store and monitor the waste until it’s ready for disposal.
Wastewater discharges into a river, lake or other natural water source can pollute the surrounding ecosystem and harm aquatic life. The contaminated water can also enter drinking water supplies and pose health risks to people.
Liquid waste disposal must take into account a variety of factors, including the proximity of the facility to local residents and surface water sources. It’s also important to keep in mind the potential for a pipeline leak or other accidents that could impact the public.
Disposal
The disposal of liquid waste is a complex process that requires special handling and treatment. Incorrect disposal can lead to environmental pollution, public health risks, and ecological damage. However, with proper management, you can minimize these problems. Liquid waste disposal involves the safe treatment, recycling, and disposal of chemical substances that have harmful effects on the environment. It also includes the systematic handling and disposal of domestic sewage, industrial effluents, and other hazardous liquid wastes. The process is regulated by government agencies to ensure the safety of humans and the environment.
The type of liquid waste you produce can determine the disposal method you choose. Some liquid wastes are less toxic and need only light treatment, while others require more aggressive treatments. In addition, the disposal site needs to have the proper soil formation and stability. Softer soils can allow waste to shift and leak, which may necessitate a different disposal technique. In addition, you will need to consider the cost of different methods and choose one that fits your budget.
A few of the most popular techniques for liquid waste disposal include sludge digestion, landfilling, and incineration. Each of these methods has its own benefits and disadvantages. Sludge digestion can help you reduce the amount of waste your facility produces, while landfilling can result in increased greenhouse gases. Incineration, on the other hand, is an effective but costly way to dispose of liquid waste. It releases toxic pollutants into the atmosphere and can cause air quality issues, exacerbate asthma and other respiratory conditions, and contribute to climate change.
Proper liquid waste disposal is important for businesses, because it protects the environment and prevents legal liabilities. It is also heavily regulated, and even small infractions can incur hefty fines. Liquid wastes are an unavoidable byproduct of many industrial processes, and they can contain dangerous chemicals and toxins that can pose a threat to human health and the environment.
Liquid wastes are produced by a number of industries, including oil and gas, mining, manufacturing, and pharmaceuticals. They can be contaminated with a variety of pollutants, including heavy metals and organic compounds, which can pose serious health hazards. In addition, these materials can also contaminate water sources, such as rivers, lakes, and groundwater.
Storage
The way in which liquid waste is stored has a huge impact on both the environment and human health. If it is improperly disposed of, it can contaminate water sources and cause severe health issues for humans and animals. To avoid such problems, it is essential to follow best practices when storing liquid waste. The first step is to identify the type of liquid waste. Ignitable wastes are those that have a flash point below 60°C or 140°F, and corrosive wastes are those that can eat through metal. Other common categories of liquid waste include flammable wastes, toxic chemical wastes, and reactive wastes.
Once the type of liquid waste is determined, it is important to select a disposal site that complies with local regulations and guidelines. Choosing a site with good soil formation and stability is also important, as loose soils may allow the waste to shift or leak. The disposal site should also be located away from any surface water sources. A nearby well water source could cause contaminated runoff to seep into the water supply, which is a serious threat to human and animal health.
It is also important to store liquid waste in a secure, leak-proof container that is compatible with the type of waste. For example, acid that corrodes metal should not be stored in metal containers. If it is not possible to safely store the liquid waste on-site, it should be transported by a professional waste management company. When transporting the waste, it is critical to ensure that it is clearly labeled and that it has a proper lid. Lastly, it is important to leave 1-2” of head space in the container to reduce the risk of spills.
Another option for storing and disposing of liquid waste is to send it to a facility that specializes in turning non-hazardous liquid waste into compost. This method is less expensive than other types of disposal and can benefit the environment by providing beneficial nutrients for crops and plants. If your facility is interested in trying this method, contact a waste treatment company to learn more about their services.
Regulations
Businesses that generate liquid waste have a duty to ensure it’s dealt with in a compliant manner. That includes those generating sewage effluent as well as manufacturing waste. The latter could include oils – both edible and motor varieties, paints, containers of chemicals or solvents and battery acid.
Sewage and liquid wastes need to be disposed of through a public sanitary sewer system or sewage disposal system (SDS) that has been constructed, maintained and operated in accordance with the approval of the permit-issuing official. If the SDS does not meet the requirements, the facility may be required to perform pretreatment on the sewage/liquid waste before it is discharged.
Occupational safety is also a priority when it comes to the handling of hazardous liquid waste. Workers are susceptible to burns, injuries and illnesses when dealing with such waste, and it’s important to minimize those risks as much as possible. Using best practices in the handling, storage and transportation of liquid waste helps businesses achieve these goals.
Inadequate liquid waste management can have devastating impacts on the environment and on people’s health. It can also have economic consequences, including fines and legal challenges. Luckily, there are numerous companies that specialize in safe and responsible handling of liquid waste, helping businesses comply with all relevant regulations.
The Resource Conservation and Recovery Act (RCRA) is the primary law governing household, commercial and industrial solid and liquid waste. It sets standards for the collection, storage, treatment, recycling and disposal of both hazardous and non-hazardous waste.
Other federal laws that affect liquid waste management include the Clean Water Act (CWA) and the Safe Drinking Water Act (SDWA). The CWA establishes water quality standards, while the SDWA ensures drinking water is free from contaminants.
The SDWA also regulates the storage and discharge of wastewater into U.S. waters, as well as the use of treated wastewater for irrigation. It sets standards for sludge disposal and imposes requirements on industrial wastewater dischargers.